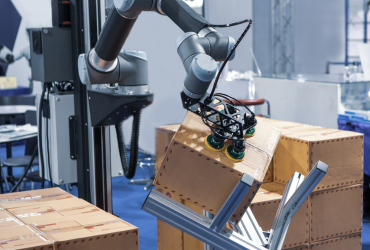
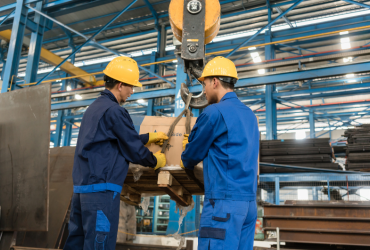
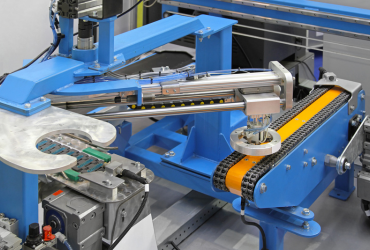
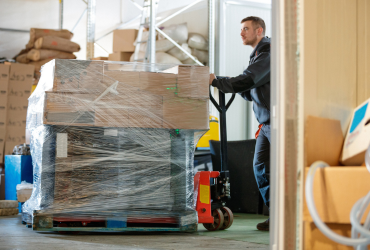
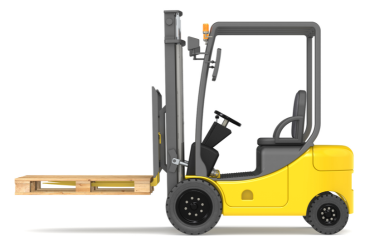
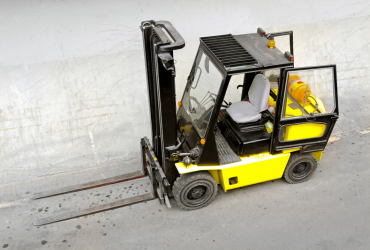
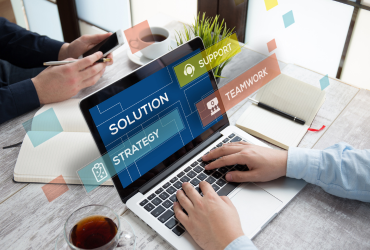
Welcome to the Ultimate Guide to Effective Material Handling Solutions
Developed by MAS – Manufacturing Automation Solution Company:
Manufacturing Automated Solutions (MAS) is a leader in material handling technologies. This article highlights some of MAS experiences in this comprehensive guide, and explores the latest trends and best practices in material handling.
Streamlining Your Operations for Optimal Efficiency. In today’s fast-paced and competitive business environment, efficiency is key to success. And when it comes to material handling, maximizing productivity and reducing costs are paramount.
Whether you are running a warehouse, a manufacturing facility, or a retail operation, having the right material handling solutions is essential. From automated conveyor systems to advanced inventory tracking technologies, there are a variety of tools and strategies available to streamline your operations and optimize efficiency.
We will delve into topics such as warehouse layout and design, equipment selection, inventory management, and process optimization. By implementing some of the strategies outlined in this guide, you will be able to improve your material handling processes, enhance productivity, cut costs, and ultimately gain a competitive edge in your industry. Are you ready to take your operations to the next level? Let’s get started.
Importance of Efficient Material Handling
Efficient material handling is crucial for any business that deals with physical goods. It involves the movement, storage, and control of material throughout the supply chain. Effective material handling can have a significant impact on your bottom line, improving productivity, reducing errors, and minimizing costs.
One of the key benefits of efficient material handling is increased productivity. By optimizing your processes and reducing unnecessary steps, you can improve the speed and accuracy of your operations. This means quicker turnaround times, faster order fulfillment, and ultimately, happier customers.
In addition to productivity gains, efficient material handling can also help reduce costs. By utilizing the right equipment and processes, you can minimize waste, avoid damage to goods, and optimize space utilization. This leads to lower operational costs and improved profitability. The ideal scenario is trying to eliminate in process inventory accumulated after individual steps in the process of manufacturing or packaging of your product.
MAS has developed technologies such as automatic process buffering to be able to accumulate the product in case of the stop of downstream equipment. When the problem is eliminated, the automatic buffer transfers product back into a stream.
MAS developed flexible programmable systems, designed to eliminate change over time, when equipment is stopped to convert machinery to a different size or model for the product or packaging material.
Furthermore, effective material handling can enhance the safety of your operations. By implementing proper handling procedures and utilizing ergonomic equipment, you can reduce the risk of injuries and create a safer working environment for your employees.
Implementing efficient material handling practices also allows you to adapt to changing market demands more easily. MAS has been introducing new tools for advancing flexibility of automatic machinery by providing complete programmability of the mechanical and control hardware to accomplish programmable convertibility of automatic systems for product change over.
Using MAS developed technology for streamlined processes and flexible equipment; you can quickly adjust your operations to accommodate fluctuations in demand, changing product requirements, or new market trends.
In summary, efficient material handling is essential for improving productivity, reducing costs, enhancing safety, and adapting to market changes. By investing in the right material handling solutions, you can optimize your operations and gain a competitive advantage.
Common Challenges in Material Handling
While efficient material handling offers numerous benefits, there are also common challenges that businesses face in this area. Understanding and addressing these challenges is crucial to achieving optimal efficiency. Let’s explore some of the most common challenges in material handling.
One of the major challenges is poor warehouse layout and design. Inefficient layouts can result in wasted space, longer travel distances, and increased labor costs. It is essential to design your warehouse in a way that minimizes unnecessary movement and maximizes space utilization.
Another challenge is the lack of proper equipment. Using outdated or inadequate equipment can hinder productivity and increase the risk of errors or accidents. Investing in modern, reliable, and appropriate material handling equipment is essential for efficient operations.
Inventory management is another area where businesses often face challenges. Poor inventory control can lead to stockouts, overstocking, or inaccurate inventory records. Implementing robust inventory management systems and processes is crucial for efficient material handling.
Furthermore, ineffective process optimization can hinder efficiency. Businesses need to analyze and optimize their material handling processes regularly. This involves identifying bottlenecks, streamlining workflows, and continuously improving operations.
Lastly, lack of employee training and engagement can pose challenges. Proper training ensures that employees are competent in their roles and understand how to handle material efficiently. Engaging employees in the improvement process can also boost morale and foster a culture of continuous improvement.
Overcoming these challenges requires a proactive approach and a commitment to continuous improvement. By addressing these common challenges, businesses can streamline their material handling operations and achieve optimal efficiency.
Types of Material Handling Equipment
One of the key elements of effective material handling is choosing the right equipment for your operations. There is a wide range of material handling equipment available, each designed for specific tasks and environments. Let’s explore some of the most common types of material handling equipment.
- Forklifts: Forklifts are versatile and widely used equipment for lifting and moving heavy loads. They are available in various sizes and configurations to suit different applications. Forklifts can be powered by electricity, diesel, or gas, depending on the specific requirements of your operations.
- Conveyor Systems: Conveyor systems are an essential component of many material handling operations. They automate the movement of goods throughout your facility, reducing manual handling and increasing efficiency. Conveyor systems can be customized to suit different layouts and requirements.
- Pallet Jacks: Pallet jacks, also known as pallet trucks, are used for moving palletized loads. They are compact and maneuverable, making them ideal for tight spaces. Pallet jacks can be manual or electric, with electric models offering additional features such as power-assisted lifting.
- Automated Guided Vehicles (AGVs): AGVs are autonomous vehicles that can transport material without human intervention. They are commonly used in large-scale operations where repetitive material movement is required. AGVs can be programmed to follow predefined routes and perform tasks such as picking, transporting, and sorting.
- Racking Systems: Racking systems are used for storing goods in a systematic and organized manner. They maximize vertical space utilization and facilitate efficient inventory management. Common types of racking systems include selective racks, drive-in racks, and push-back racks.
- Sortation Systems: Sortation systems are used to sort and divert items based on specific criteria, such as destination or product type. They can be integrated with conveyor systems and other material handling equipment to automate the sorting process.
These are just a few examples of the many types of material handling equipment available. When selecting equipment for your operations, it is important to consider factors such as load capacity, maneuverability, maintenance requirements, and compatibility with existing systems.
Choosing the right equipment can significantly enhance the efficiency of your material handling processes, so take the time to evaluate your needs and invest in high-quality equipment that meets your requirements.
Key Considerations When Choosing Material Handling Solutions
When it comes to choosing material handling solutions, there are several key considerations to keep in mind. Making informed decisions based on these considerations will ensure that you select the most suitable solutions for your operations. Let’s explore some of the key factors to consider.
- Operational Requirements: Start by evaluating your operational requirements. Consider factors such as the types of material you handle, the volume of goods, the layout of your facility, and any specific challenges or constraints you may have. This will help you identify the most suitable material handling solutions for your needs.
- Equipment Reliability and Durability: Look for equipment that is reliable and durable. Material handling equipment is subjected to demanding conditions and heavy use, so it is important to invest in high-quality equipment that can withstand the rigors of your operations.
- Compatibility and Integration: Consider the compatibility and integration capabilities of the material handling solutions you are considering. Ensure that the equipment can seamlessly integrate with your existing systems and processes. This will minimize disruptions and maximize the efficiency of your operations.
- Scalability and Flexibility: Choose material handling solutions that offer scalability and flexibility. Your business needs may change over time, and it is important to have solutions that can adapt to these changes. Scalable and flexible solutions will allow you to accommodate growth, new product lines, or changes in demand without major disruptions to your operations.
- Safety Features: Prioritize safety when selecting material handling solutions. Look for equipment that is designed with safety features such as anti-collision systems, ergonomic designs, and operator training programs. Safety should always be a top priority in material handling operations.
- Total Cost of Ownership: Consider the total cost of ownership when evaluating material handling solutions. This includes not only the initial purchase price but also factors such as maintenance costs, energy consumption, and potential downtime due to several factors including stops, recovery time, change over time for another model and breakdowns. Choosing solutions with lower total cost of ownership will contribute to long-term cost savings.
These are just a few key considerations to keep in mind when choosing material handling solutions. It is also important to consult with experts in the field, conduct thorough research, and assess the specific needs of your operations before making a decision. Investing time and effort in the selection process will pay off in the long run.
Implementing an Effective Material Handling Process
Implementing an effective material handling process requires careful planning and execution. It involves analyzing your current processes, identifying areas for improvement, and implementing solutions to streamline operations. Let’s explore the key steps involved in implementing an effective material handling process.
- Evaluate Current Processes: Start by evaluating your current material handling processes. Identify bottlenecks, inefficiencies, and areas for improvement. This can be done through observation, data analysis, and feedback from employees.
- Set Objectives: Establish clear objectives for your material handling process. These objectives should be specific, measurable, attainable, relevant, and time-bound (SMART). For example, your objective could be to reduce order processing time by 20% within six months.
- Develop a Plan: Develop a comprehensive plan to achieve your objectives. This plan should include specific actions, timelines, and responsibilities. Break down the plan into manageable tasks and allocate resources accordingly.
- Invest in Technology: Leverage technology to streamline your material handling processes. This can include implementing inventory management systems, adopting barcode or RFID tracking technologies, or utilizing automation solutions such as conveyor systems or AGVs. Choose technologies that align with your objectives and operational requirements.
- Optimize Warehouse Layout: Assess your warehouse layout and make necessary changes to optimize space utilization and minimize unnecessary movement. Consider factors such as product flow, equipment placement, and ergonomic considerations. A well-designed warehouse layout can significantly improve efficiency and reduce costs.
- Train and Engage Employees: Provide comprehensive training to your employees on the new processes, equipment, and technologies. Engage them in the improvement process and encourage their feedback and suggestions. Employees who are well-trained and engaged are more likely to embrace changes and contribute to the success of the material handling process.
- Monitor and Continuously Improve: Implement metrics and key performance indicators (KPIs) to monitor the effectiveness of your material handling process. Regularly review these metrics and identify areas for further improvement. Continuously seek feedback from employees and stakeholders to identify new opportunities for optimization.
Implementing an effective material handling process is an iterative and ongoing effort. It requires a commitment to continuous improvement and a willingness to adapt to changing needs and technologies. By following these steps and fostering a culture of efficiency, you can achieve optimal material handling operations.
Streamlining Operations for Optimal Efficiency
Streamlining your material handling operations is crucial for achieving optimal efficiency. It involves eliminating unnecessary steps, reducing waste, and optimizing workflows. Let’s explore some strategies for streamlining your material handling operations.
- Standardize Processes: Standardize your material handling processes to ensure consistency and efficiency. Develop standard operating procedures (SOPs) that outline the best practices for various tasks and ensure that employees follow these procedures. Standardization reduces variability and improves predictability.
- Implement Lean Principles: Apply lean principles to identify and eliminate waste in your material handling processes. This can include eliminating unnecessary movement, reducing waiting time, and minimizing inventory. Lean principles focus on continuous improvement and the elimination of non-value-added activities.
- Utilize Just-in-Time (JIT) Inventory Management: Implement just-in-time inventory management to reduce excess inventory and minimize storage costs. JIT inventory management ensures that material are received and used only when needed, reducing the risk of stockouts and overstocking.
- Leverage Automation: Automate repetitive and time-consuming tasks to improve efficiency. This can include implementing conveyor systems, AGVs, or automated picking and sorting solutions. Automation reduces manual handling, minimizes errors, and increases throughput.
- Optimize Material Flow: Analyze the flow of material within your facility and identify areas where bottlenecks occur. Optimize material flow by reorganizing workstations, adjusting process sequences, or implementing parallel processing. A smooth and efficient material flow improves productivity and reduces lead times.
- Implement Continuous Improvement Initiatives: Foster a culture of continuous improvement by encouraging employees to identify and implement small changes that lead to incremental improvements. Implementing a formal continuous improvement program, such as Kaizen or Six Sigma, can help drive ongoing improvement efforts.
- Collaborate with Suppliers and Customers: Strengthen collaboration with your suppliers and customers to optimize material handling operations. This can involve sharing demand forecasts, coordinating delivery schedules, or implementing vendor-managed inventory (VMI) programs. Collaboration reduces lead times, minimizes stockouts, and improves overall supply chain efficiency.
By implementing these strategies, you can streamline your material handling operations and achieve optimal efficiency. Remember that streamlining is an ongoing process, and it requires a commitment to continuous improvement and an openness to embracing new technologies and methodologies.
Technology and Automation in Material Handling
Technology and automation play a significant role in enhancing the efficiency of material handling operations. Advancements in technology have revolutionized the way material are handled, tracked, and managed. Let’s explore some of the key technologies and automation solutions used in material handling.
- Inventory Management Systems: Inventory management systems utilize software and hardware to track and manage inventory levels, locations, and movement. These systems provide real-time visibility into inventory, automate ordering processes, and facilitate accurate inventory forecasting.
- Barcode and RFID Tracking: Barcode and radio frequency identification (RFID) technologies are used to track and identify individual items or containers. They enable automated data capture, reduce manual data-entry errors, and improve inventory accuracy and traceability.
- Automated Conveyor Systems: Automated conveyor systems transport material throughout a facility using motorized belts, rollers, or chains. They eliminate the need for manual material handling, reduce labor costs, and increase throughput. Conveyor systems can be customized to suit different layouts and requirements.
- Automated Guided Vehicles (AGVs): AGVs are autonomous vehicles that can navigate and transport material without human intervention. They are commonly used in large-scale operations where repetitive material movement is required. AGVs can be programmed to follow predefined routes and perform tasks such as picking, transporting, and sorting.
- Warehouse Management Systems (WMS): Warehouse management systems integrate various material handling processes and technologies into a centralized platform. They optimize inventory storage, enable efficient order
For over 30 years MAS has been developing programmable systems capable to seamlessly convert from handling one product to another virtually without any down time. These solutions are based on utilizing a universal mechanical design with programmable servo-driven devices and robotics, to construct standard material handling machines.
MAS is offering multiple types of material handling and packaging systems,
including programmable case erectors, programmable product conveyors, pallet dispensers, pallet roller and chain conveyors, flexible palletizing systems, shrink wrapping systems with corner boards and top seal film, flexible labeling systems and many more.
MAS is providing Flexible Automation Solutions for material handling that require frequent changes for various models of products.